MECHANICAL SEALS
Home / Mechanical Seals
In modern industrial applications, mechanical seals play a critical role in ensuring the efficiency, reliability, and safety of various equipment. Whether in pumps, compressors, or other rotating machinery, mechanical seals prevent the leakage of fluids and gases, thus maintaining system integrity and minimizing downtime. Their design and functionality make them a vital component in industries ranging from oil and gas to pharmaceutical manufacturing.
A mechanical seal is a device designed to join two systems or components together while preventing leakage. Unlike traditional sealing methods such as packing or gaskets, mechanical seals offer superior sealing performance, particularly in applications with high pressure, temperature, and speed.
- Single Spring Seals
- Multi Spring Seals
- Conical Spring Seals
- Single Cartridge Seals
- Double Cartridge Seals
- Metal Bellow Seals
- Single Dry Seals
- Single BH Seals
- Double Seals
- ANFD Double Seals
- Rotary Joints
- Grundfos Seals
- SS & MS GLR C-Clamps
- SS Metal Bellows
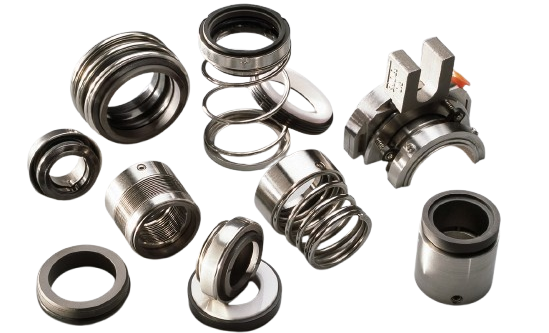
Single Spring Seals

One of the most used mechanical seals in industrial settings is the single spring seal. These seals are well-known for their dependability, affordability, and adaptability in a range of settings. They are perfect for low- and medium-duty applications because of their single helical spring construction, which guarantees consistent pressure on the sealing surfaces.
- Rotating Seal Face: Attached to the shaft, it rotates with the equipment.
- Stationary Seal Face: Mounted on the housing, it remains stationary.
- Single Coil Spring: Provides the axial force needed for sealing.
- Elastomer O-Ring: Ensures a tight seal between the components.
- Set Screws: Secure the seal assembly to the shaft.
Multi Spring Seals
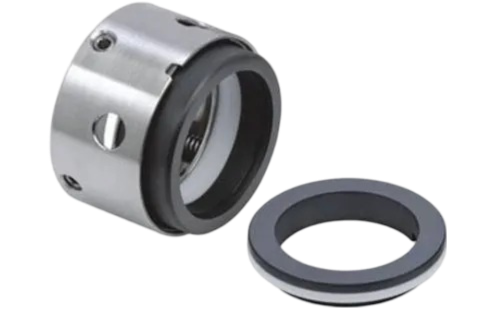
Multispring seals are sophisticated mechanical seals made for demanding industrial applications that require accuracy, dependability, and adaptability. In contrast to single spring seals, multispring seals distribute stress evenly on the sealing faces by using several smaller springs spaced evenly around the shaft. Their performance is improved by this design, which makes them perfect for corrosive, high-temperature, and high-pressure settings.
- Rotating Seal Face: Mounted on the shaft, it rotates with the equipment.
- Stationary Seal Face: Fixed to the housing, providing a static sealing surface.
- Multiple Springs: Evenly distributed around the shaft, these springs ensure consistent axial force.
- Elastomer O-Rings: Provide a flexible and leak-proof seal between components.
- Metal Retainer: Holds the springs and seal faces in place, ensuring structural integrity.
Conical Spring Seals
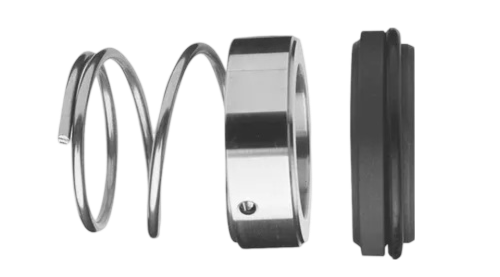
Conical spring seals are a specific kind of mechanical seal that improves sealing performance in a range of industrial applications because of their distinctive spring geometry. Conical spring seals, as opposed to conventional helical or multispring seals, use a tapered spring that lowers clogging and offers a constant axial force. This design is particularly useful for working with fluids that are slurry-like, abrasive, and viscous.
- Rotating Seal Face: The face attached to the rotating shaft.
- Stationary Seal Face: The static face mounted on the housing.
- Conical Spring: A tapered spring that provides axial force and resists clogging.
- Elastomer O-Rings: Ensure a tight seal and accommodate minor misalignments.
- Retainer and Fasteners: Hold the seal assembly together and secure it to the shaft.
Single Cartridge Seals
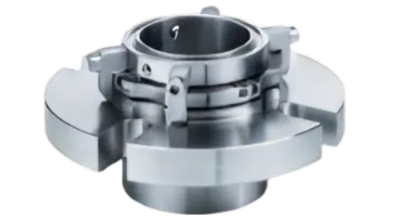
One kind of mechanical seal system that is intended for simple installation, dependable operation, and low maintenance is the single cartridge seal. These are pre-assembled systems that come with a single housing that houses all the required parts, including gland plates, O-rings, springs, and seal faces. Single cartridge seals are a popular option for many sectors since they make installation easier and lower the possibility of mistakes.
- Rotating Seal Face: Mounted on the shaft and rotates with it.
- Stationary Seal Face: Fixed to the gland plate and provides a sealing surface.
- O-Rings and Gaskets: Provide a leak-proof seal between components.
- Spring Mechanism: Maintains consistent axial pressure on the seal faces.
- Cartridge Housing: Holds all the components together as a single unit.
- Gland Plate: Secures the seal assembly to the pump or equipment.
Double Cartridge Seals

Double cartridge seals are a cutting-edge mechanical sealing technology made to deliver exceptional sealing capabilities in challenging industrial settings. Double cartridge seals, as opposed to single seals, use two sets of sealing faces, providing improved leak protection and the capacity to withstand high-pressure, abrasive, or toxic fluids. Their compact, pre-assembled design ensures dependable performance in crucial applications while making installation and maintenance easier.
- Primary Seal (Process Side): Prevents the leakage of the process fluid.
- Secondary Seal (Atmosphere Side): Provides an additional barrier to contain any leakage from the primary seal.
- Barrier Fluid System: Circulates a buffer or barrier fluid between the seals to provide cooling, lubrication, and pressure balancing.
- Seal Faces: Made from materials such as silicon carbide or tungsten carbide for durability and resistance to wear.
- O-Rings and Gaskets: Ensure a tight seal between components and prevent fluid leakage.
- Cartridge Housing: Holds all the components in a single, compact unit.
Metal Bellow Seals

High-performance mechanical seals called metal bellow seals are made especially to withstand harsh environments including high temperatures, caustic chemicals, and high pressures. These seals offer exceptional flexibility, endurance, and resilience to a variety of industrial difficulties because they use a flexible, corrugated metal bellow as a spring element. Their special design provides a more durable and dependable sealing solution by doing away with the requirement for conventional springs.
- Metal Bellow: The core component, typically made from materials like Inconel, Hastelloy, or stainless steel, offering flexibility and corrosion resistance.
- Seal Faces: Often crafted from hard materials such as silicon carbide or tungsten carbide for durability and wear resistance.
- O-Rings and Gaskets: Provide additional sealing between the metal bellow and the equipment.
- Gland Plate: Secures the seal to the pump or other rotating equipment.
Single Dry Seals
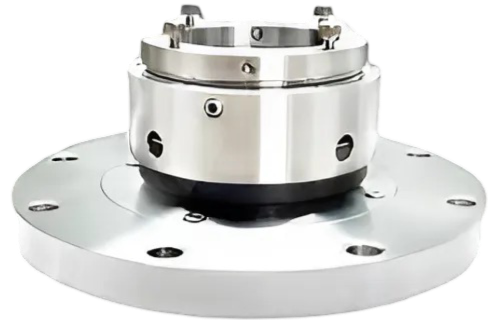
For a variety of industrial applications, single dry seals provide a dependable, effective, and contamination-free sealing solution. Long-term dependability and economical operation are guaranteed by their straightforward design, high-performance materials, and precise engineering. You may reduce downtime and achieve optimal performance by choosing the appropriate seal for your application and adhering to recommended maintenance procedures.
- Rotating Seal Face: Attached to the rotating shaft, this component moves in unison with the equipment.
- Stationary Seal Face: Fixed to the housing, it remains stationary while providing a sealing interface with the rotating face.
- O-Rings or Elastomers: Provide secondary sealing and prevent leakage between the seal components.
- Spring Mechanism: Applies axial force to maintain contact between the rotating and stationary faces.
- Seal Housing: Encases the seal components and provides a secure connection to the equipment.
Single BH Seals
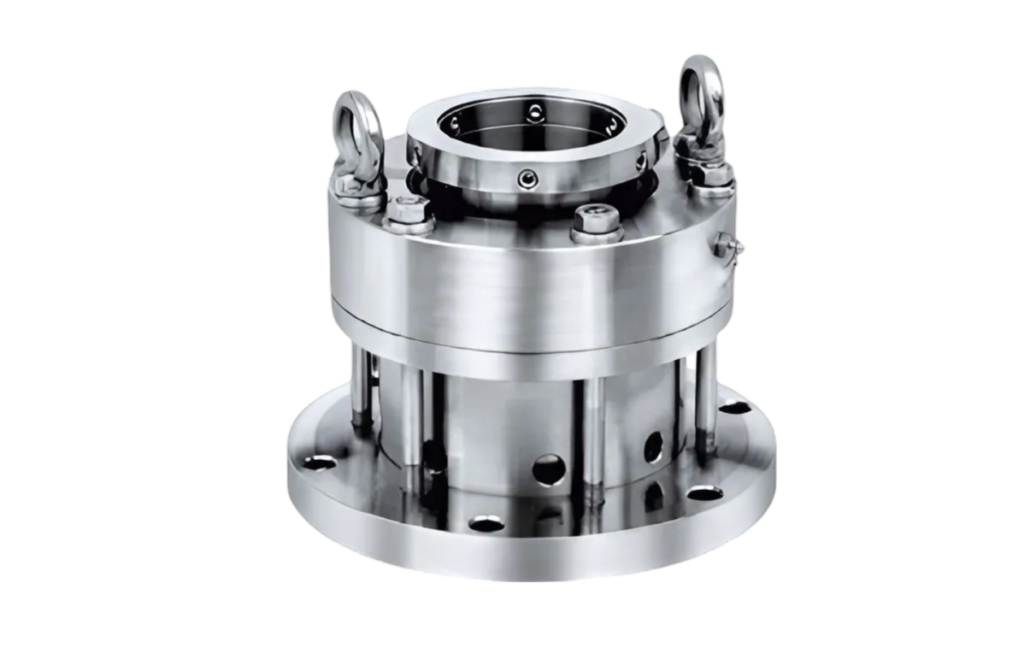
Single BH seals (Balanced Hydraulic seals) are mechanical seals designed to offer high reliability and efficiency in applications involving moderate to high pressure. These seals are typically used in rotating equipment such as pumps, mixers, and compressors, where they provide an effective barrier against fluid leakage while maintaining consistent performance under varying operating conditions.
- Primary Seal Face: The rotating component that comes into contact with the stationary face to create a seal.
- Stationary Seal Face: Mounted to the housing, it remains stationary while forming a tight seal with the rotating face.
- O-Rings and Elastomers: Provide secondary sealing and ensure a leak-free connection between the seal components.
- Spring Mechanism: Maintains axial pressure on the seal faces, ensuring consistent contact and sealing performance.
- Seal Housing: Encloses the seal assembly and connects it to the rotating equipment.
Double Seals

Double seals offer a cutting-edge way to stop leaks and guarantee that machinery operates well across a variety of industries. They are a vital component of contemporary industrial processes because of their capacity to withstand high temperatures, pressures, and hazardous compounds. You may greatly increase equipment reliability, decrease downtime, and prolong the life of your gear by choosing the best double seal for your application and keeping the optimum operating conditions.
- Rotating Seal Faces: Attached to the shaft, these faces rotate and come into contact with stationary seals to create a fluid-tight barrier.
- Stationary Seal Faces: Mounted to the housing, these faces remain stationary while forming a secure seal with the rotating faces.
- Elastomers (O-Rings): These provide additional sealing between components and prevent leaks at the junctions.
- Spring Mechanism: Ensures constant pressure on the seal faces, maintaining a consistent seal during operation.
- Seal Housing: Encases the seal assembly and ensures secure installation into the equipment.
ANFD Double Seals

For industries that need high-performance machinery in harsh settings, ANFD double seals provide a sturdy and dependable sealing solution. They are perfect for vital industries including chemical processing, oil and gas, power generation, and pharmaceuticals because of their capacity to withstand high-pressure, high-temperature, and chemically demanding applications. ANFD double seals can improve overall safety, save maintenance costs, and increase operational efficiency by comprehending the application requirements and choosing the appropriate materials.
- Rotating Seal Face: This face is mounted on the rotating shaft and creates a dynamic sealing surface when in contact with the stationary face.
- Stationary Seal Face: The stationary face is mounted to the housing and remains in place while creating a tight seal with the rotating face.
- Elastomers/O-Rings: These are used to seal the gaps between the rotating and stationary parts, preventing fluid leakage.
- Springs: Springs maintain the appropriate axial pressure on the seal faces, ensuring consistent sealing performance.
- Seal Housing: The housing holds the seals in place and ensures proper alignment within the equipment.
Rotary Joints Seals

In systems where fluids or gases are transferred between fixed and rotating parts, rotary joint seals are essential parts. Their main duty is to stop leaks, which guarantees the secure and effective operation of machinery in a variety of sectors. Rotating joint seals offer a dependable solution for crucial fluid handling applications in a variety of industries, including power generation, chemical processing, food manufacturing, and aerospace.
- Rotating Part (Rotor): The rotor is the rotating component to which the seal is attached. It is typically connected to a shaft or another rotating element in the system.
- Stationary Part (Stator): The stationary part is connected to the housing or support structure and does not move. The seal is mounted here to ensure no fluid leakage between the rotating and stationary parts.
- Seal Elements: These include mechanical seals or lip seals that create a barrier between the rotor and stator, preventing fluid from leaking.
- Bearings: Rotary joints often include bearings to support the rotating part and reduce friction during operation.
- End Caps: These are used to close off the housing, ensuring the proper sealing environment for the rotary joint.
- O-Rings and Gaskets: These components help to ensure a tight seal and prevent any fluid leakage.
Grundfos Seals

For pump systems in a variety of industries to operate dependably and effectively, Grundfos seals are essential parts. Grundfos offers a variety of seal types, including mechanical seals, lip seals, O-rings, and cartridge seals, to satisfy the particular requirements of various applications. Grundfos seals contribute to lower maintenance costs and better system performance by stopping leaks, increasing pump efficiency, and prolonging equipment service life.
- Rotating Part (Rotor): The rotor is the rotating component to which the seal is attached. It is typically connected to a shaft or another rotating element in the system.
- Stationary Part (Stator): The stationary part is connected to the housing or support structure and does not move. The seal is mounted here to ensure no fluid leakage between the rotating and stationary parts.
- Seal Elements: These include mechanical seals or lip seals that create a barrier between the rotor and stator, preventing fluid from leaking.
- Bearings: Rotary joints often include bearings to support the rotating part and reduce friction during operation.
- End Caps: These are used to close off the housing, ensuring the proper sealing environment for the rotary joint.
- O-Rings and Gaskets: These components help to ensure a tight seal and prevent any fluid leakage.
SS Metal Bellows

In a variety of industrial applications, stainless steel bellows are essential parts that offer flexibility, durability, and sealing qualities. They are perfect for challenging conditions because of their exceptional strength, resistance to corrosion, and capacity to withstand pressure and movement. SS metal bellows provide a dependable and durable way to guarantee the effectiveness and security of your systems, regardless of your industry—aerospace, chemical processing, automotive, or power generation.
- Flexibility: SS metal bellows can expand and contract, making them ideal for absorbing motion and accommodating thermal expansion or pressure variations.
- Corrosion Resistance: The use of stainless steel ensures excellent protection against rust, oxidation, and chemical corrosion, which makes these bellows suitable for aggressive environments.
- Durability: Stainless steel bellows are known for their long lifespan, providing reliable service even in challenging conditions.
- Sealing Efficiency: SS metal bellows are often used in sealing applications due to their ability to maintain an airtight or watertight seal, even under varying pressures and temperatures.
- Customization: SS metal bellows can be manufactured to meet specific operational requirements, including custom dimensions, pressure ratings, and temperature tolerances.